Now We Offer a NEW, Better Ductile Iron - POWER DUCTILE™
Power Ductile™ is our own proprietary ductile iron chemistry, and it has drastically improved mechanical properties compared to 100-70-03 grade ductile iron, which is the industry standard for high performance cylinder sleeves. We have also developed our own heat treatment to ensure that we are able to achieve and maintain a material strength that is far beyond the standard in the industry.
As compared to 100-70-03, Power Ductile™ has improved tensile strength, yield strength, elongation, and hardness. It is superior in every way to the standard ductile iron for cylinder sleeves.
Drag Racers, Tractor Pullers, and anyone else operating under extreme, high horsepower conditions stand to benefit by switching to Power Ductile for their cylinder sleeve needs. We highly recommend it!.
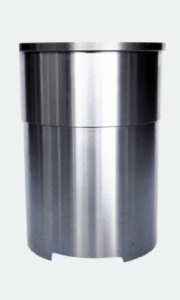
Virtually Any Material
Having your own foundry has its advantages. We can cast virtually any ferrous material that you can find in the ASTM manuals or dream up yourself (but try not to get carried away). As a result, our cylinder liners are always the highest quality available anywhere. You can view a simple breakdown of some of our more common material here (pdf).
Why Use Ductile Iron Cylinder Sleeves
Ductile Iron is a specific type of cast iron which has an addition of magnesium to it to make the graphite in it nodular. You can think of the graphite as little globes instead of the flake structure that is typical with your regular gray iron.
The nodules strengthen the material in a couple of ways. They add to the tensile strength of the iron and they also increase its impact resistance. Ductile iron also has an elongation factor in it that allows the material to “flex” somewhat inside the bore. This is the “bend but don’t break” advantage of ductile iron over cast iron in your cylinder liner.
Ductile iron engine cylinder sleeves are the standard in the high-performance engine world, for engine builders that are producing high horsepower and highly boosted engines that are generating a lot of torque.
Ductile iron looks like this:
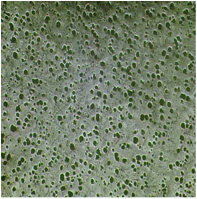
Whereas gray iron looks like this under a microscope:
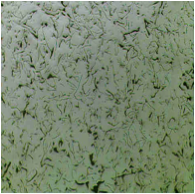
Why do my sleeves need to be made from centrifugally cast material?
The centrifugal casting process involves pouring molten metal into a spinning die and allowing the metal to solidify over time while the die continues to rotate at a high velocity. The metal is literally spun to the outside of the die, leaving a hole in the center and ultimately creating a cylindrical metal tube.
Centrifugal castings are superior to static castings because the casting process results in a more consistent crystalline structure in the metal, drastically reducing the potential for casting defects and impurities in the metal. Through the effect of the g-force applied to the metal, heavier metal is spun to the exterior of the tube and any impurities essentially “float” to the inside diameter of the casting, and are machined away.
Why Buy Sleeves From PowerBore?
In addition to machining all of our cylinder sleeves in our facility in Salem, Ohio, we also pour all of our own centrifugal castings in our foundry just across the street. We are literally a one-stop shop for cylinder sleeves. We control everything from material to finished sleeves, which results in higher quality, shorter lead times, and competitive prices.